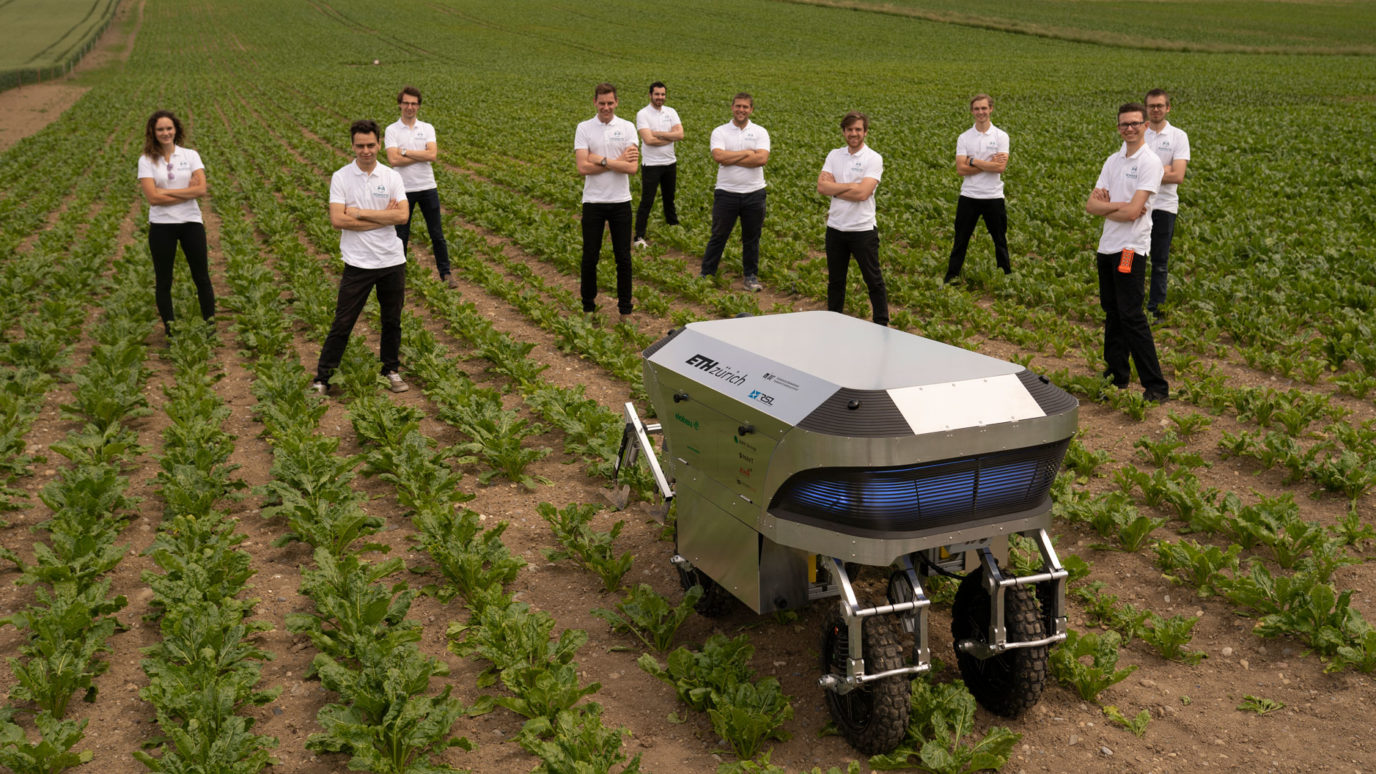
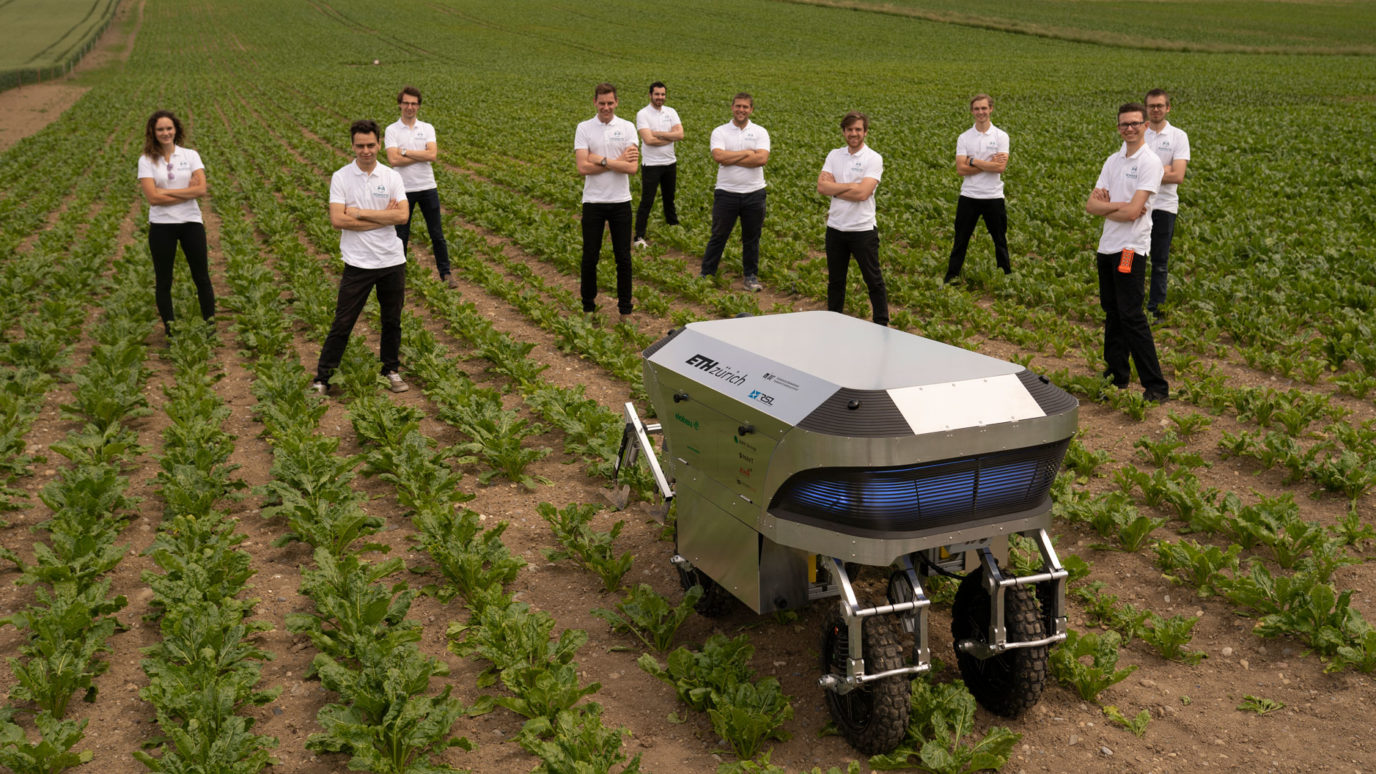
The ETH Zurich focus project Rowesys, supported by elobau, impressively shows the possibilities of digitalization and smart technology to minimize damage on humans and nature. With this goal in mind, ten motivated students have been working on the development of the agricultural robot «Rosie» since last September. They were supported by eight expert coaches and many sponsors.
To demonstrate the concept of herbicide-free weeding by Rowesys, a prototype was developed for sugar beet fields where herbicide use is currently particularly high. The requirements that an agricultural robot has to meet are manifold. In addition to efficiency, reliability, autonomy and safety, user-friendliness is a particularly important aspect. Rosie was developed with these points in mind. But how does the weeding work in detail and what makes the prototype special?
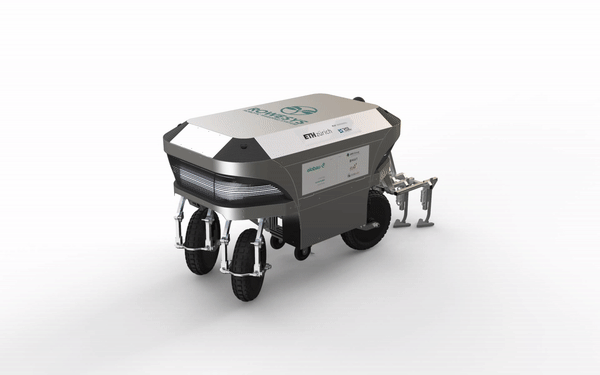
For mechanical weeding, Rosie pulls four small ploughshares through the soil at a depth of 2-3cm between the rows. This separates the weeds from the roots and transports them to the surface where they dry out.
Rosie is powered by four powerful wheel hub motors that have enough traction to pull the ploughs through the soil and negotiate slopes of up to 15 degrees. Each wheel is equipped with a self-developed spring-damper system that allows the plough to overcome obstacles and guarantees that all wheels are in contact with the ground at all times. This not only prevents the robot from getting stuck, but also ensures a stable platform with balanced weight distribution to reduce ground compression. Each wheel can also be steered individually and independently. This gives the system maximum flexibility and allows various manoeuvres, such as rotating in place to navigate to the next row. Thanks to two powerful batteries, the robot operates completely emission-free.
A futuristic casing was developed to protect Rosie from adverse weather. Together with an electronics box, this protects the sensitive components from rain and dust. The entire system is IP54 splash water and dust protected.
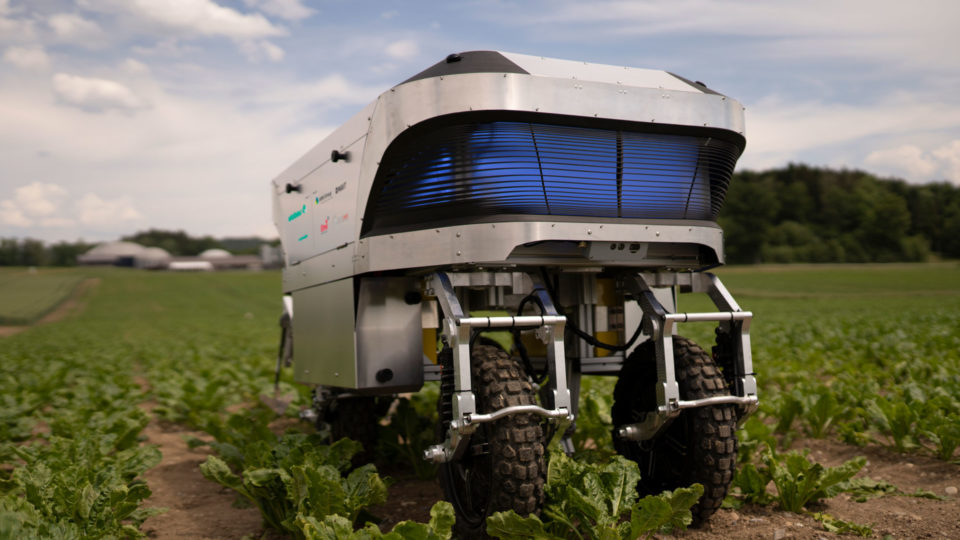
In addition to the hardware, the robot has a sophisticated software. Several camera sensors and a powerful on-board computer enable Rosie to distinguish between sugar beet and weeds and navigate autonomously through the rows. The end of the row is automatically detected and the system navigates to the next unprocessed row. No GPS positions of the seedlings or pre-programmed routes are required, minimising the farmer’s effort.
Intuitive controls, which allow switching between manual and autonomous operation, ensures user-friendly operation. The operation of the system can be learned in a short time. Status lights and a voice output show the user the current status of the system at all times. Safety is also considered. In addition to a radio emergency stop, the robot also has four emergency stop systems developed by elobau. The system can be brought to a standstill at any time in a dangerous situation.
The prototype is currently in the test phase. In the field, the hardware and software are being tested for reliability under various conditions and optimized on a daily basis. With each autonomously weeded row, the goal of herbicide-free agriculture moves one step closer.
Comments
write a comment