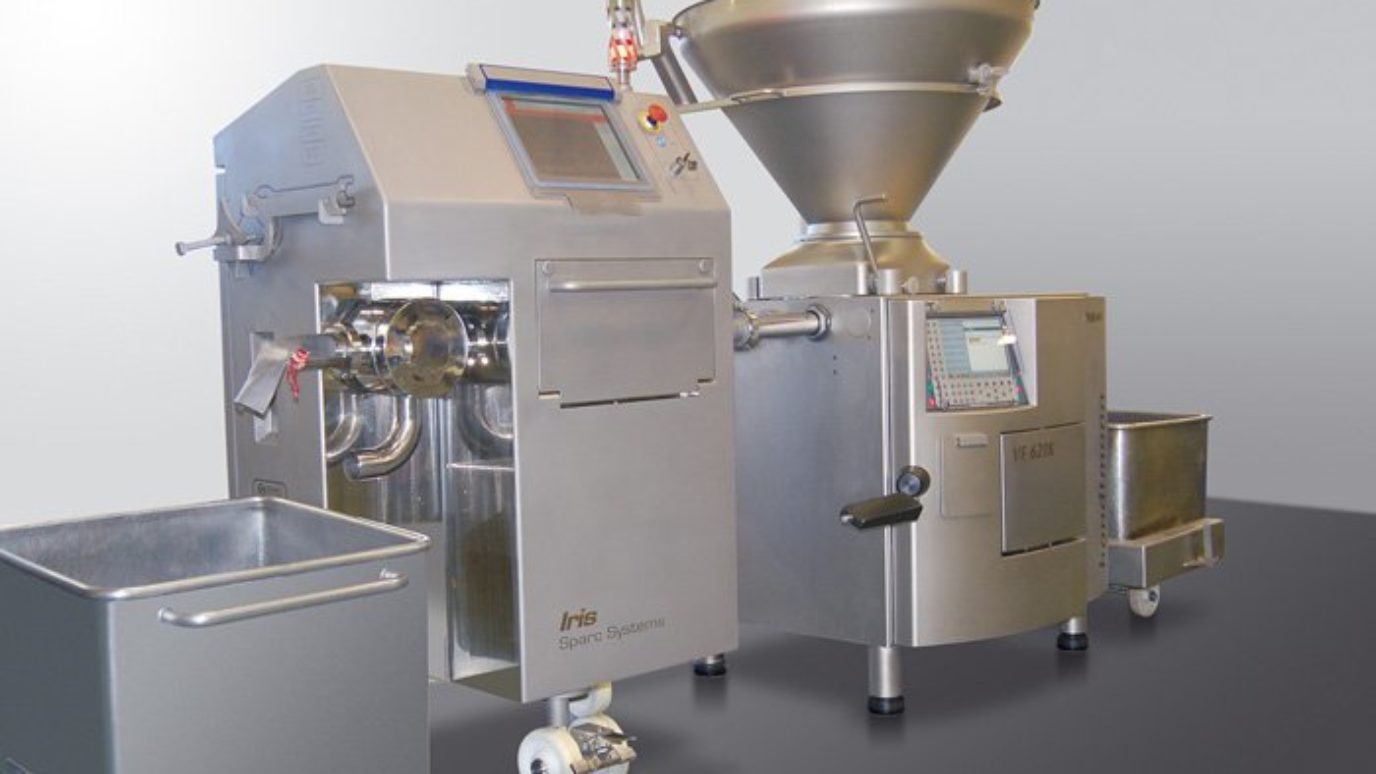
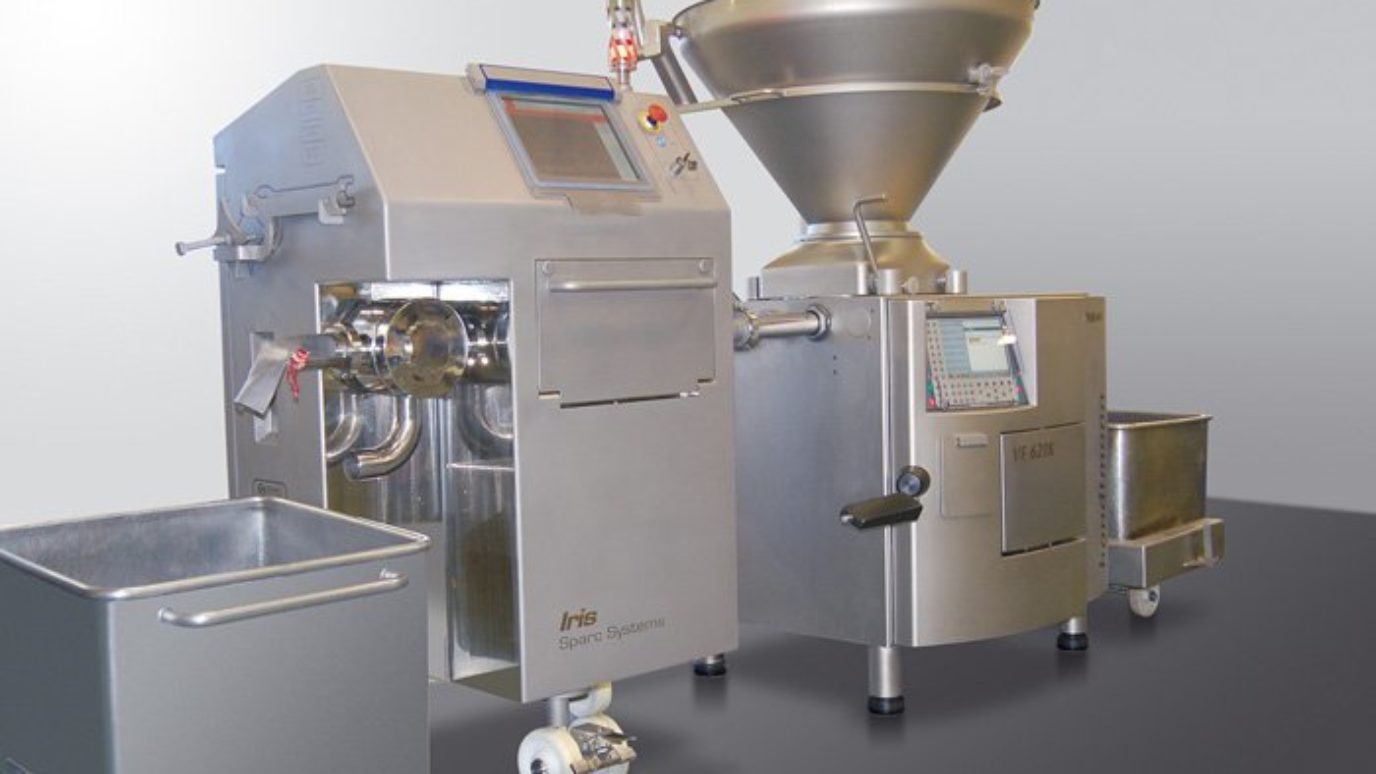
The IRIS Pipeline Inspection System is one of a number of high quality inspection machines from Sparc Systems. It promotes systematic product flow and delivers optimal detection of contaminants, while reducing the amount of product rejected. The Iris has been designed to address the unique requirements posed by products flowing through a pipe. It also helps manufacturers comply with stringent HACCP protocols and food safety requirements.
Sparc Systems are renowned for their innovative approach to machine building, and when they sought to make further enhancements to the Iris system, with a view to reducing cost and improving operational performance, they turned to machine safety experts’ elobau for their assistance in simplifying the complex electrical system.
Sparc’s solution was to redesign the printed circuit board in such a way it would replace the entire control panel ‘hard’ wiring. The PCB would be required to have mounting facilities for key machine control and safety components which would have simple ‘plug & play’ features. The key design elements of the new PCB were that it should be robust, safe, simple and increase machine reliability and operation.
The innovative PCB design results in a significant reduction of the wiring time by around 10 hours. It also significantly reduces material costs as a number of cable sizes and colours can be completely removed from the system, and by using simple, specific plug and socket harness wiring connections, initial component connection, subsequent field failure exchange is minimised. The new design is expected to reduce the number of man hours in building and testing by up to 50%.
The PCB is ready to go as soon as it is fitted and populated with its DIN rail mounted sub-element components (safety relay, Ethernet module, motor starter etc.). As the PCB has already been ‘circuit approved’ during the design phase, every PCB produced will effectively be ‘pre-tested’ for functionality, which helps to eliminate wiring faults and reduces electrical and functional testing by around 2-4 hours. Once the pre-wired looms connecting the PCB to the main operational components of the machine (motors, encoders etc.), have been plugged in, full machine testing can be completed.
Every machine is fully tested for functional and operational performance before leaving the factory at Sparc, meaning they are effectively commissioned prior to dispatch. Again, this makes it ‘plug & play’ for the customer to install, commission and maintain the equipment at site. For operational purposes, fault finding has been reduced to individual sub-element level, which minimises machine downtime. Incoming and outgoing connections are segregated into separate high and low power zones, reducing interference between power and communication systems.
When it came to selecting the machine safety components needed to finalise the complete safe system, having worked with elobau previously and knowing that they could provide the quality and reliability required, Sparc involved elobau in the project. Following discussions on the design, elobau provided working samples of their recommendations to the Sparc design team to test each component for compatibility. After rigorous testing, four elobau products were chosen to facilitate the simple ‘plug & play’ approach required for the new machine:
• The 171 series M30 PBT safety switch, having an integral M8 socket. Used where basic safety functions were required.
• The 122MSV series M12 stainless steel safety switch, having an integral M12 socket and IP 6K9 rating. For use where the switch may come into contact with the processed product, and be subjected to high pressure and high temperature cleaning.
• The 363 series ‘intelligent’ safety switch interface unit, allowing up to 4 safety switches to be connected to each relay safe input, whilst also providing 4 individual control outputs for PLC monitoring.
• The 470 series safety relay, with plug and socket connection, completes the safe system.
Through the innovative application of their products, elobau helps their customers build machinery that sets the industry standards for performance, their ease of use, and reliability and safety. Sparc Systems is a global leader in the design and manufacture of Weighing, Inspection, Counting and Bespoke Systems for the Food, Pharmaceutical and Packaging industries. Both Sparc and elobau, recognise the true value and benefits of working together and supporting each other – a partnership that works.
Comments
write a comment