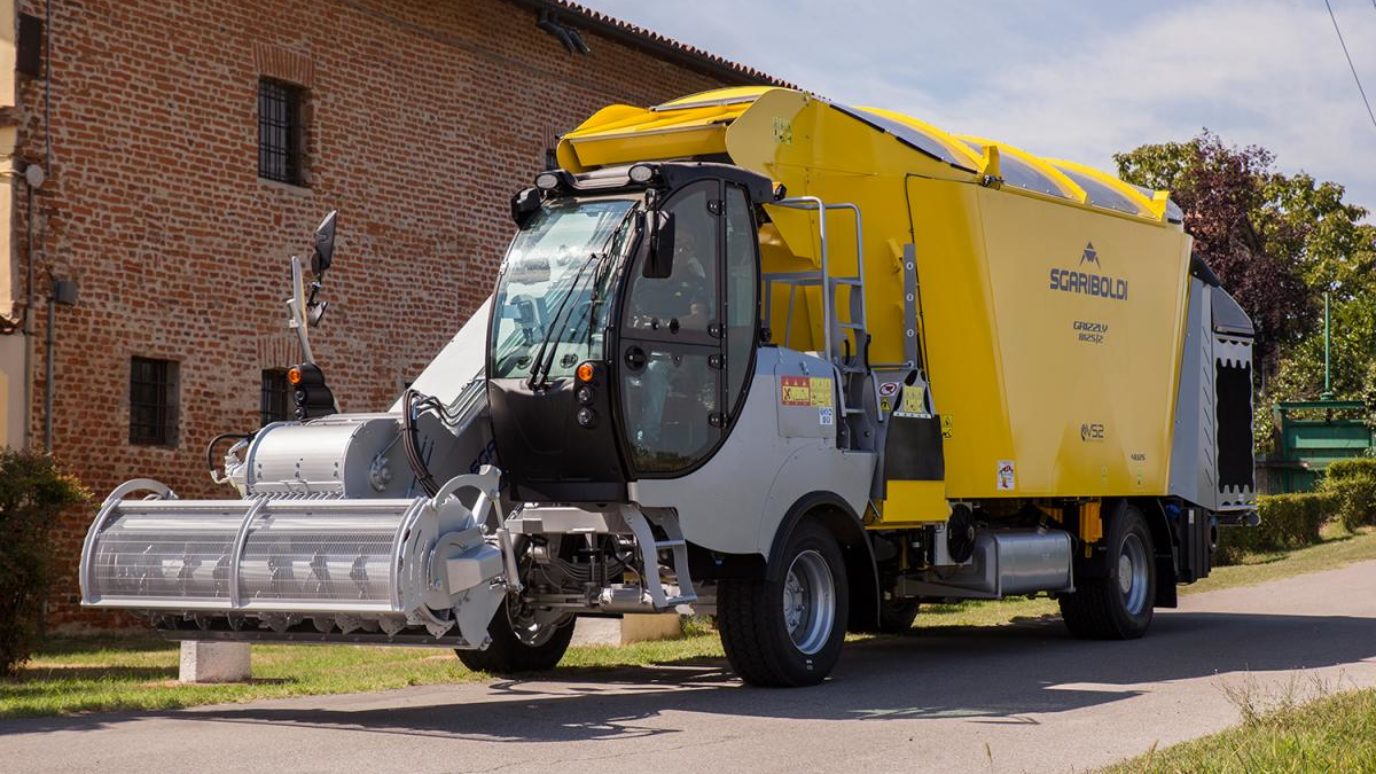
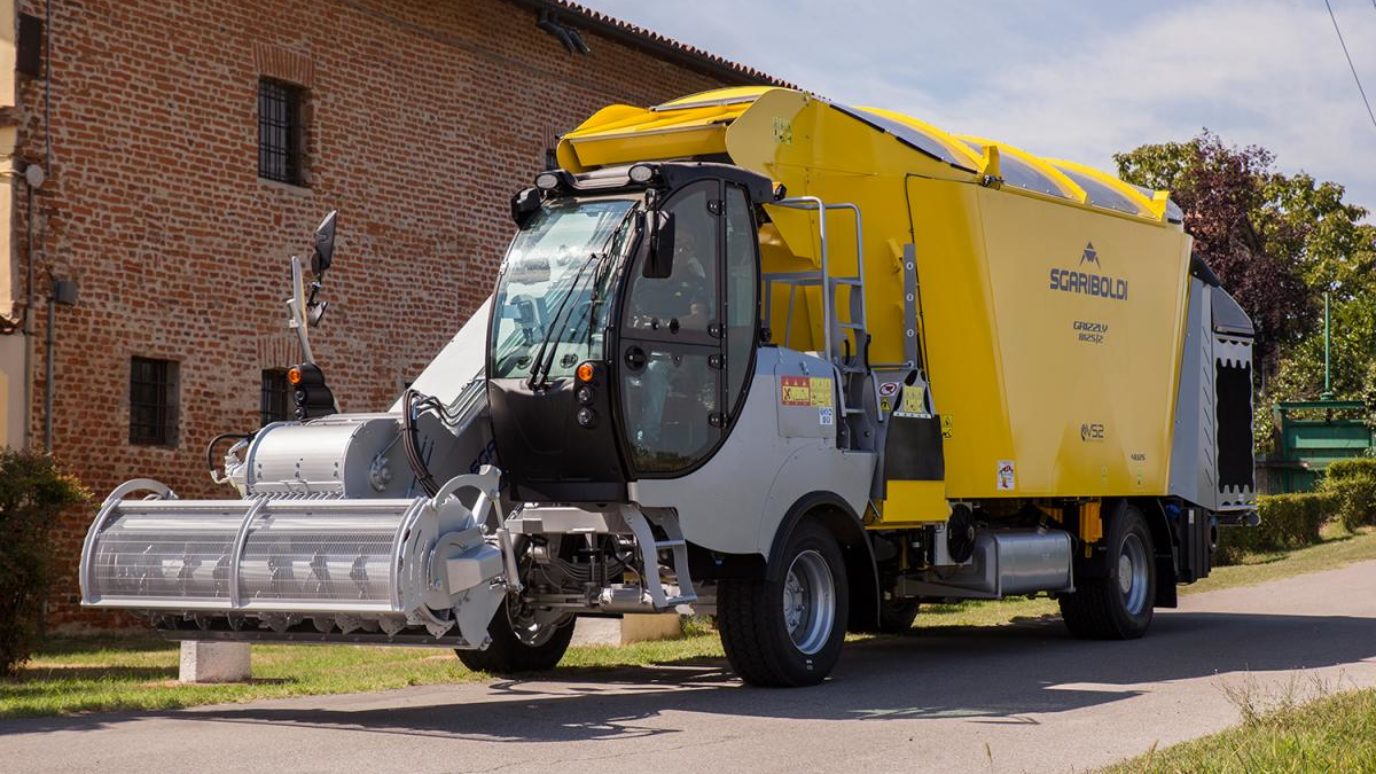
Animal feeding via joystick
Traditional sectors such as agriculture benefit enormously from technology and innovations. This is because every innovation can potentially simplify work steps and streamline processes, resulting in farmers regaining something they usually have very little of… Time. The manufacturer Sgariboldi specialises in machines for livestock breeding and provides feed mixer wagons that simplify the day-to-day work of farmers. The Italian company first introduced a self-propelled machine back in 1987. This enabled several work steps to be combined into one. Since then, Sgariboldi has continuously developed its products and has always relied on state-of-the-art technologies.
All stages of the feeding process can be controlled from the cab of the self-propelled Italian machine: collecting, cutting, mixing and distributing the daily rations. The feed mixer wagons have a high workload of up to 14 hours a day, 365 days a year.
Sgariboldi's Titanum Series
Development objective
The most technologically advanced cockpit
Two years ago, Sgariboldi decided to develop the I-CAB 2, the most technologically advanced, high-performance cab yet. The aim was to provide more interior space, clearer visibility and a larger display, combining all control elements within reach of the operator. The I-CAB 2 was not only designed for a particular model but can also be integrated into all self-propelled Sgaribold series 6000, 7000 and 8000 machines.
The development goal was to achieve the best possible performance from the machine with the cockpit installed – so that the operator saves time regardless of their skill set. The performance level should be repeated, i.e. at the same performance every day.
The operator controls in the vehicle cab play an important role in this. Originally, the operator controls in the I-CAB 2 were intended to be different products from elobau’s operator control range, building on a long-standing partnership between the two manufacturers.
But this plan changed when the agricultural machinery manufacturer learned about the new 225MA midi armrest from elobau. It combines all the necessary functions in one system. The concept: elobau offers customised operator controls in a modular system. All the modules in the system have already been tested and certified in line with standards. This saves customers time and money when it comes to development, testing and certification. The armrest consists of several modules, each of which can be individually configured: joysticks and hand throttle, operating unit, armrest and storage compartment, hitchwheel and potentiometer. The buttons can be assigned as required. The operator controls have background and function illumination. The respective symbols are printed on the buttons in an abrasion-resistant way. These modules are EU 167/2013 standard (Mother Regulation) compliant.
All requirements combined
The modular Armrest 225MA midi
With the 225MA midi, not only are all the vital operator controls available, but the ergonomic design allows the operator to work without getting tired. The multifunctional armrest therefore perfectly matched the concept of the new cockpit by Sgariboldi. In these new cockpits, almost all of the main machine functions are controlled by the operator via the 225MA midi. These include the tiller, auger, mill, unloading and all other functions. For example, the boom cutter arm is raised and lower during the loading process by the integrated J2 joystick. The right and left movement of the joystick starts the rotation of the cutting unit. During unloading, the unloading flap can be opened and closed with the J2. The conveyors that support the unloading process can be moved from right to left with a joystick, while the encoder controls the speed of the active conveyors.
To control the engine speed, Sgariboldi has also integrated the hand throttle into the armrest. In addition, any relevant functional messages are displayed clearly to the operator.

Ergonomically perfect
All operator controls within reach
By using the 225MA midi, Sgariboldi were also able to overcome a challenge normally associated with technology. “It is absolutely vital that the operator has the perfect feel for moving the boom or cutting arm with the joystick. But this movement cannot really be modelled linearly,” explains Luca Sgariboldi, Managing Director of Sgariboldi. This is because the milling arm reacts with a delay when the joystick is moved. But the elobau armrest solved this. “The 225MA midi allows the precise curve of the required boom response to be plotted for each machine,” says Sgariboldi. Thanks to the ergonomics of the armrest, all the operator controls are within easy reach. The symbols on the control elements help the driver of the feed mixer wagon to find their way around the machine more quickly.
However, the 225MA midi not only makes things easier for the operator. It is also much easier for engineers! Consequently, Sgariboldi now has a system that can be integrated into a vehicle as a plug-and-play solution – with the armrest connected to the feed mixer wagon via CAN-Bus. This allows multiple different configurations of the machine to be managed with the same wiring. Even if a retrofit on the vehicle requires new modules in the armrest, no new wiring is necessary. The plug-and-play concept does not change. Sgariboldi offers its machines in different variants – with different unloading options or with one or two protective caps. All these variants use the same software. All it takes is a parameter change via the display so that the buttons on the armrest deploy the correct actions.
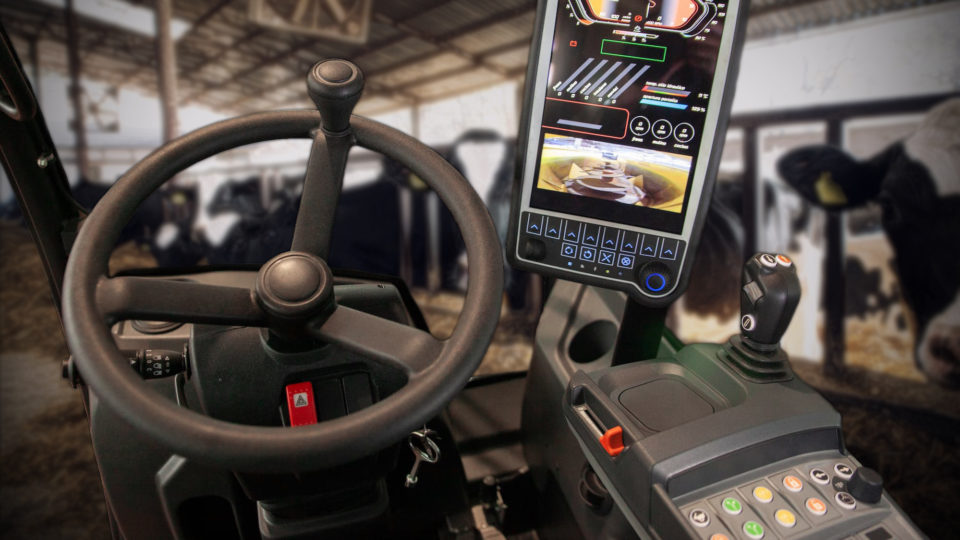
The 225MA midi was developed in accordance with the EU 167/2013 (Mother Regulation) making it ideal for agricultural machines. In addition, in any configuration, it corresponds to Agricultural Performance Level C (AgPL r c), which defines the safety level of the electronic control and operating units in agricultural machines in accordance with ISO 25119. Machine manufacturers then receive armrests and modules that have been developed and certified in accordance with these standards, often eliminating the need for time-consuming work for manufacturers or users afterwards.
It also scores points in terms of sustainability. 75% of the plastics used are bio-based plastics made from castor oil. The armrest itself is upholstered in apple leather. An additional advantage is that the modular principle makes it easy to replace individual modules in the event of repair or conversion. This saves resources. From the push buttons to the multi-function handle, customers can order all spare parts individually.
Maximum comfort and overview
The I-CAB 2
“The 225MA midi is the central component of our new cab concept,” says Luca Sgariboldi. “It ensures that the operator can control the machine with the highest level of safety and outstanding precision.” By developing the I-CAB 2, we have achieved the goals we set ourselves. The new cabin offers maximum comfort, 12% more space, significantly more brightness thanks to the large glass surfaces, has been equipped with AutoLift and now offers the operator improved air conditioning. “The seat, armrest and display are all in one unit and create a control stand that can only be compared with the largest tractors on the market,” says Sgariboldi. As manufacturers of smaller machine series do not always benefit from multiple years of research, development and testing, they are often denied access to operating systems of this level of maturity.
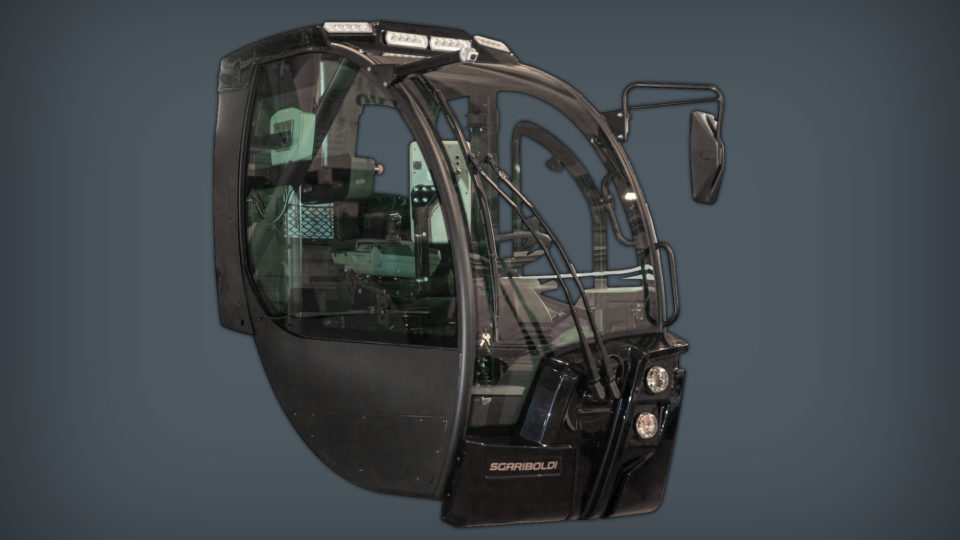
Use in extreme conditions
The armrest makes the Grizzly even more efficient
One machine that benefits from these advantages is the Grizzly 8100. The mixer was envisaged for medium-sized companies and is specially designed for continuous operation under extreme conditions. The Grizzly 8100 is designed for high-capacity lines and large volumes. The high speed at which animal feed supplies are prepared is a real added value. Thanks to the new cockpit, users can now supply animal feed even faster and more efficiently with this machine. Looking at comparable vehicles, it quickly becomes clear that the Grizzly 8100 is the undisputed leader in terms of the speed of feed preparation and cutting precision.
The development of the I-CAB 2 was also rapid. Sgariboldi was able to complete the project in a year – thanks to the good partnership with elobau. Even the switch to 100% remote work due to the pandemic did not cause a delay. “The I-CAB 2 is now our flagship,” emphasises Luca Sgariboldi. In a relatively short project time, the new cockpit enabled us to develop the top technology in the market for this type of machine.
The I-CAB 2 has proven its worth in the field and has never let machine operators down, even during long working hours and in difficult working conditions.
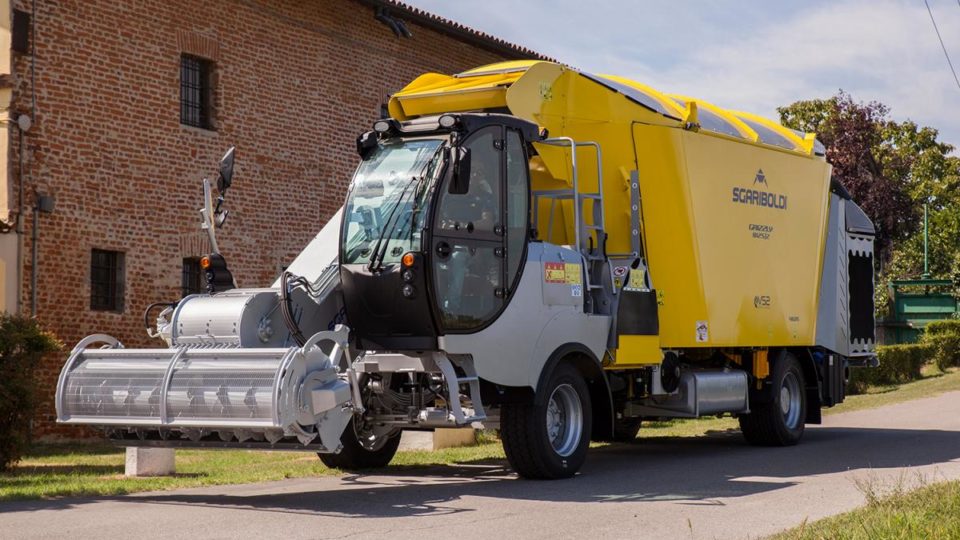
Comments
write a comment