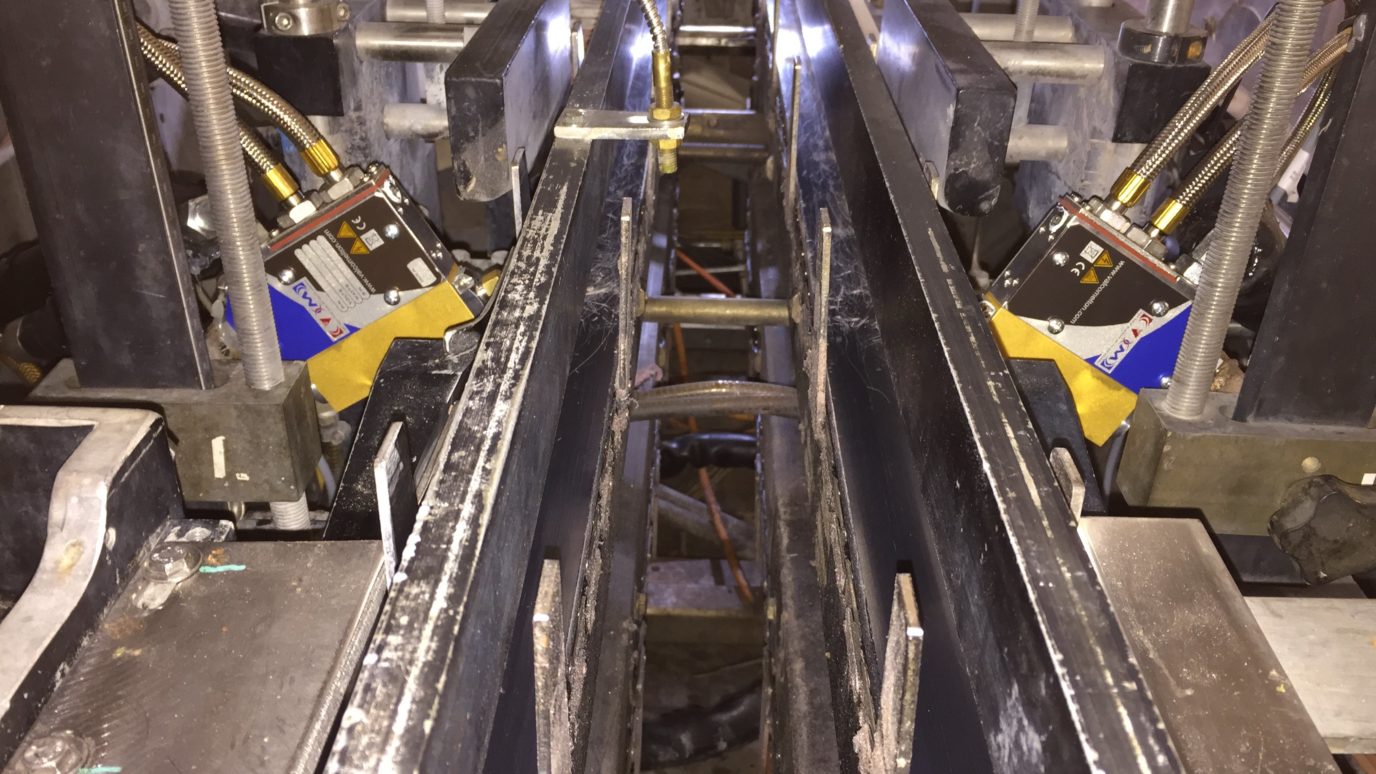
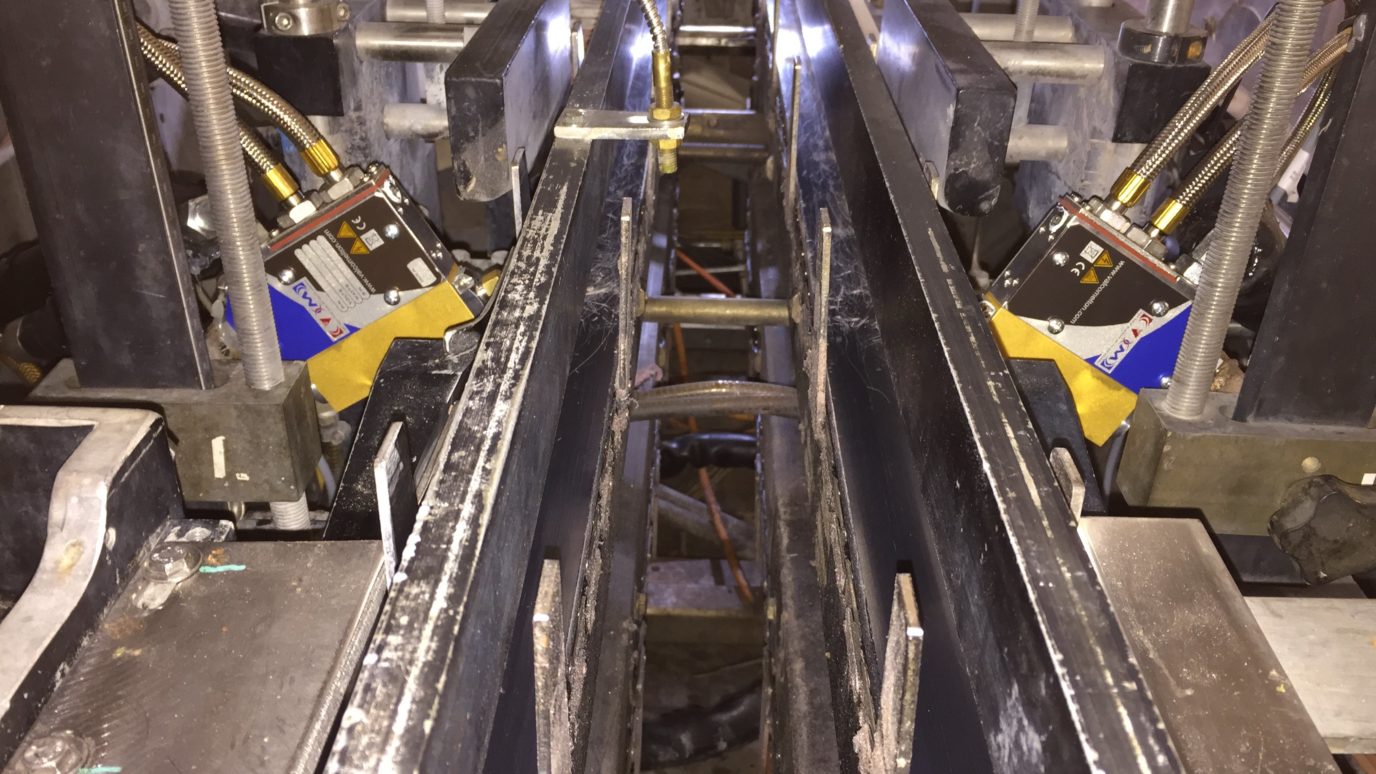
Die NiMCO Corporation ist ein führender amerikanischer Hersteller von Maschinen zum Formen, Füllen und Verschließen von Kartons und hat seinen Sitz in Crystal Lake (Illinois). NiMCO wurde 1962 gegründet, als die Milchpackung von einem wachsbeschichteten auf einen heißsiegelfähigen, kunststoffbeschichteten Pappkarton umgestellt wurde. Das Unternehmen entwickelte eine Kartonaufricht- und Bodenverschließmaschine für die kleinen Molkereien, die bereits Abfüll- und Versiegelungsanlagen betrieben. 1965 erweiterte NiMCO sein Angebot um eine neue Füll- und Verschließmaschine als Ergänzung für seine Bodenformmaschine. 1967 vermarktete NiMCO die Form-, Füll- und Verschließmaschine Model 500, die zahlreichen mittleren und kleinen Molkereien half, zu wachsen und zu überleben.
NiMCO wurde 1972 von George L. Bachner (Diplom-Fertigungsingenieur) übernommen, und mit Unterstützung durch seine beiden Söhne, die Zwillinge Larry und Jerry, wurden viele technologische Innovationen in die Maschinen integriert, die dadurch zuverlässiger wurden und einfacher zu bedienen und zu warten waren.
Sicherheitsstandards im Wandel
Im Zuge der Weiterentwicklung der Sicherheitsstandards wurde deutlich, dass die Maschinen sicherer werden mussten, und so begann NiMCO, diese zusätzlich mit Personenschutzeinrichtungen in Form von Schutztüren mit Sicherheitsschaltern und Steuereinheiten zur Überwachung dieser Schalter auszurüsten. Außerdem wurden jetzt SPS-Systeme anstelle der früheren Steuerungssystemen eingesetzt, womit NiMCO führend bei den Verpackungsinnovationen war.
Globale Überwachung
Als NiMCO mit der Notwendigkeit konfrontiert wurde, eine Fehlersuche an dem Maschinen-Sicherheitssystem durchführen zu können, das auf seinen marktführenden Maschinen zum Formen, Füllen und Verschließen von Kartons installiert ist, wandte sich das Unternehmen an die elobau sensor technology, Inc. NiMCO setzte bereits Sicherheitsauswerteeinheiten von elobau und auch Eingangserweiterungen ein, aber diese Komponenten konnten nicht mit der Außenwelt kommunizieren. Die verwendete SPS dagegen konnte das und diese Flexibilität brauchte NiMCO auch beim Maschinen-Sicherheitssystem. Daneben galt es, den Platzbedarf des aktuellen Systems zu verringern, ohne jedoch Abstriche bei der Funktionalität machen zu müssen. Nachdem man sich mehrere Optionen angesehen hatte, entschied sich NiMCO für den Einsatz des programmierbaren elobau-Sicherheitssystems – aus mehreren Gründen. Einer davon war die Tatsache, dass die bisherigen Einheiten gut funktionierten und auch die elobau-Türsensoren verwendet wurden, woran nichts geändert werden sollte. Ein weiterer Grund war die einfache Programmierung der Sicherheitssteuerung (des eloProg-Systems) durch Programmieren von Funktionsbausteinen per Drag & Drop. Das eloProg-System ermöglichte außerdem die Kommunikation per Ethernet-IP, die auch von der SPS verwendet wurde. Auf diese Weise konnte NiMCO von jedem beliebigen Ort aus über das Internet mit beiden Systemen kommunizieren.
Neu gegenüber Alt
Robert Mensing, einer der Ingenieure für Steuerungssysteme bei NiMCO, erklärte dazu: „In früheren Systemen wurden separate Sicherheitsrelais (ebenfalls von elobau) verwendet. Durch den Übergang zu einer einzigen programmierbaren Sicherheitssteuerung wurden alle Sicherheitseingangssignal-Funktionen in ein einziges Gerät verlagert. Damit konnte die Verdrahtung zwischen separaten Sicherheitsrelais entfallen, was die Verdrahtung der Sicherheitskreise deutlich vereinfachte. Die Sicherheitssteuerung ist zudem kompakter, was Platz in der Schalttafel schafft.”
Das neue System nahm wesentlich weniger Platz in Anspruch, so dass der Ethernet-IP-Router vom oberen Rack in denselben Rackbereich verlagert werden konnte. Durch die Module und die Programmierbarkeit des eloProg-Systems wurden zudem eine höhere Funktionalität und weniger Verdrahtungsaufwand erreicht.
Weltweiter Zugriff
Da NiMCO nun nicht nur die SPS und ihre Abläufe, sondern auch das Maschinensicherheitssystem über das Internet überwachen konnte, wurde auch die Zahl der Serviceeinsätze minimiert, was sich seitdem sowohl für NiMCO als auch für seine Kunden in Form von Einsparungen bei den Reise- und Stillstandskosten bemerkbar macht. Davon abgesehen, ist dies für NiMCO natürlich auch ein hervorragendes Verkaufsargument bei der Vermarktung seiner Maschinen.
Ein weiteres Projekt
Später wurde elobau erneut von NiMCO angesprochen und gefragt, ob elobau auch eine Pigtail-Version des gegenwärtig verwendeten Türschutzschalters liefern könne. elobau war gern bereit, einem seiner besten Kunden damit aushelfen zu können, und stellte NiMCO innerhalb von 2 Monaten Prototypen zum Testen zur Verfügung.
Mensing dazu: „Die vorher verwendeten Türschalter waren Kabelversionen mit unterschiedlicher Leitungslänge. Die Kabel wurden zurück zum Hauptschaltschrank geführt. Der Austausch eines Türschalters gestaltete sich wegen der großen Kabellänge und der Kabelführung schwierig. Der neue Türschalter hat eine kurze Leitung, die zu einem M8-Stecker führt, so dass ein M8-Standardkabelsatz für die Verkabelung zur Sicherheitssteuerung verwendet wird. Damit besteht jeder Austausch eines Türschalters aus einem einfachen Abziehen und Anschließen eines Steckers.”
Durch diese Änderung am Produkt braucht NiMCO nur noch einen einzigen Sensortyp auf Lager zu haben. Früher mussten dagegen viele Typen mit unterschiedlichen Kabellängen vorgehalten werden. Außerdem wurden eventuelle Reparaturzeiten auf ein Minimum begrenzt, denn NiMCO braucht nun keine langen Kabelabschnitte mehr durch die Maschinenstruktur zu führen, falls ein Sensor beschädigt werden sollte. So können auch die Servicemitarbeiter die Anlage beim Kunden schneller wieder in Betrieb nehmen – eine Win-Win-Situation also.
Zusammenfassung
Alles in allem führte die Umstellung auf eine programmierbare Steuerung zu einer Minimierung der Produktionszeit, einer Platzersparnis in der Schalttafel und einer verbesserten Fehlersuche durch Diagnosefunktionen. Überdies wurde die Möglichkeit der Datenkommunikation zwischen dem Sicherheitssystem und der SPS geschaffen, eine Funktionalität, die mit den Sicherheitsrelais nicht zu bewerkstelligen war.
„Die Bedienung der Maschine bleibt unverändert, aber der Zeitaufwand für die Verdrahtung zwischen separaten Sicherheitsrelais entfällt. Außerdem bewirkt die einfachere Verdrahtung eine Verkürzung der Inbetriebnahmezeit und eine Senkung des Aufwands für das Debugging des Sicherheitssystems” ….. Rob Mensing.
Kommentare
Kommentar schreiben